Big teams accomplish large things.
I supported this project with my expertise in low-voltage electronics and fabrication. As a member of a small team of three, I prepared wires, soldered and tested over 200 LEDs and resistors, and prepared the access points for each web camera. In addition, I was on the PVC fabrication team, where we used molds routed out of MDF and boiling water to shape 256 PVC rods.
The installation comprises 256 PVC pods of 3 strands each: 1 for data, 1 for power, and 1 for structure. A wooden beam weighing approximately one metric ton is suspended from the array, which supports 14 video displays. The construction approach allows for nearly all of the material to be reused with no modification: few of the fourteen 20’-0” Douglas Fir beams used were cut and could be sold at a discount back to the lumber yard; the steel rigging materials were rented for the installation period, and since no holes compromised the integrity of the 768 PVC pipes, they could be donated to a non-profit housing organization and urban gardening project.
As visitors view the work in the gallery, the structure periodically scans the space with its 24 cameras. The images are then compiled and plotted onto the exhibition guide, producing a “live” catalog of the exhibition (one in which visitors often find themselves among the work.) This 50’ x 50’ suspended building-sized scanner was fabricated to present and record the MADE UP: Design’s Fictions exhibition at the Art Center College of Design’s graduate Media Design Practices program.
Winner: 2012 AIA|LA Honor Award. Finalist: 2013 Architizer A+ Award.
Images courtesy, Tim Durfee.
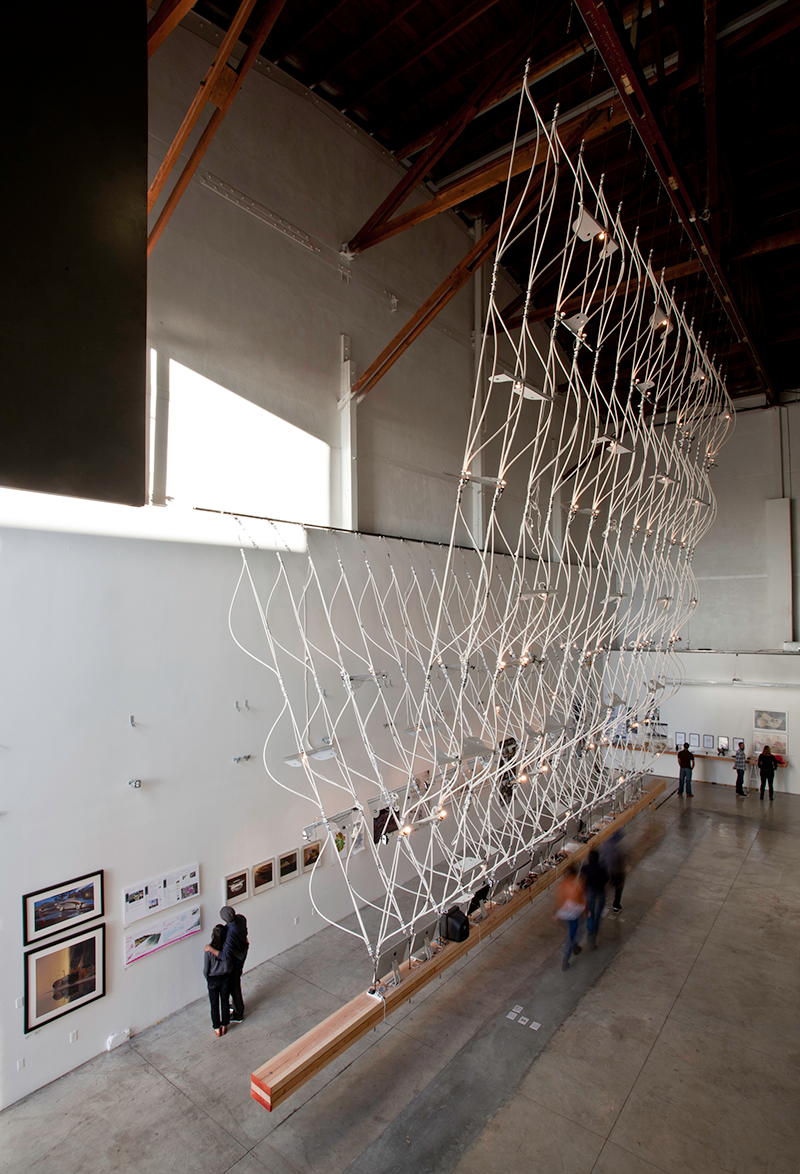
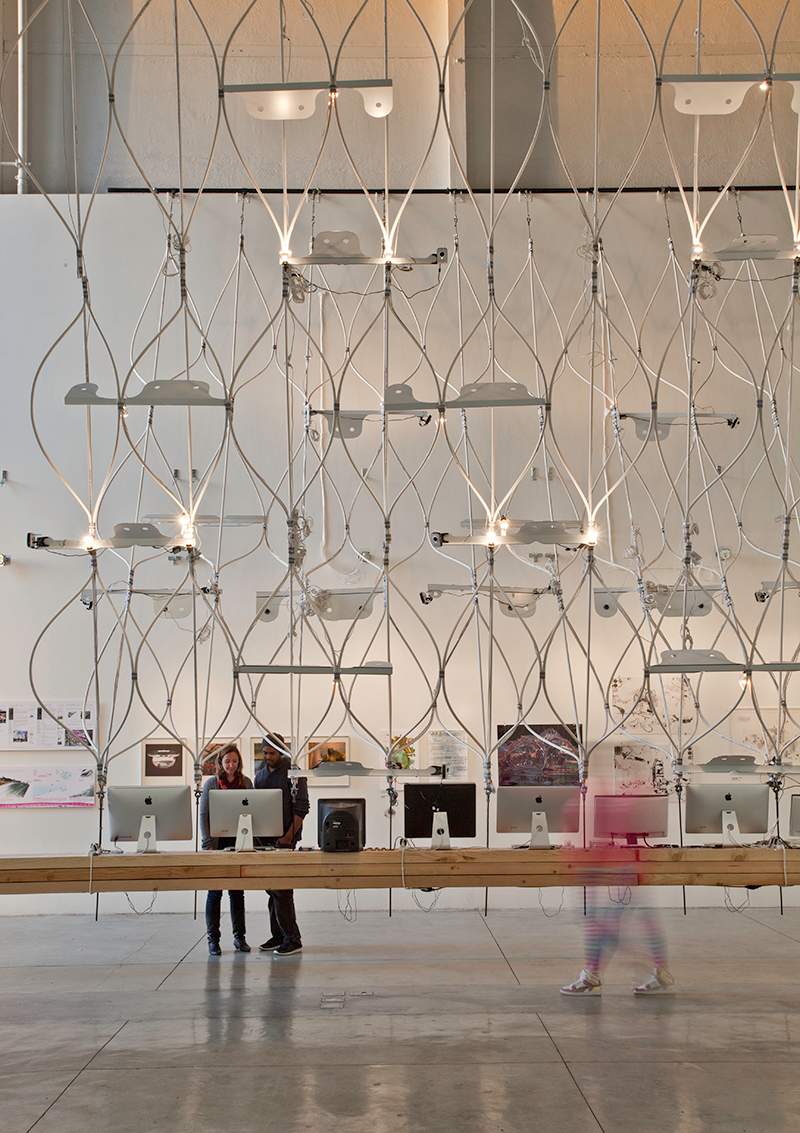
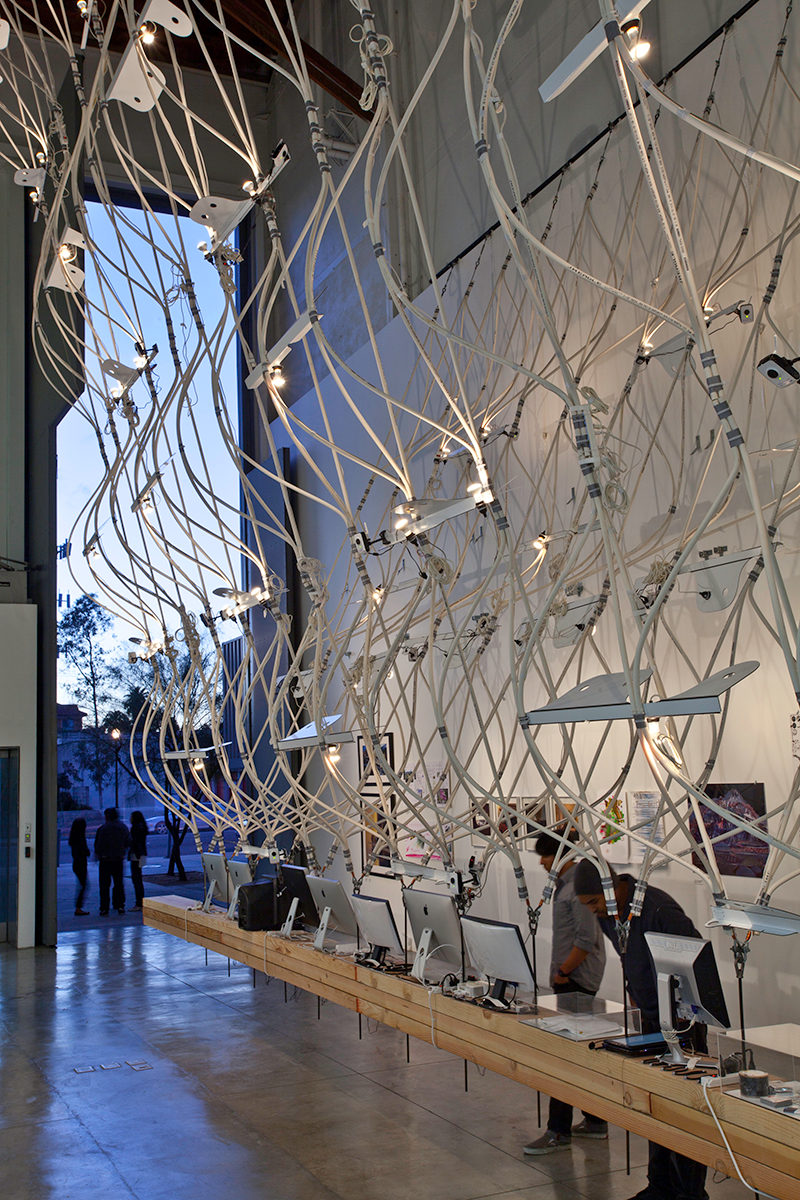
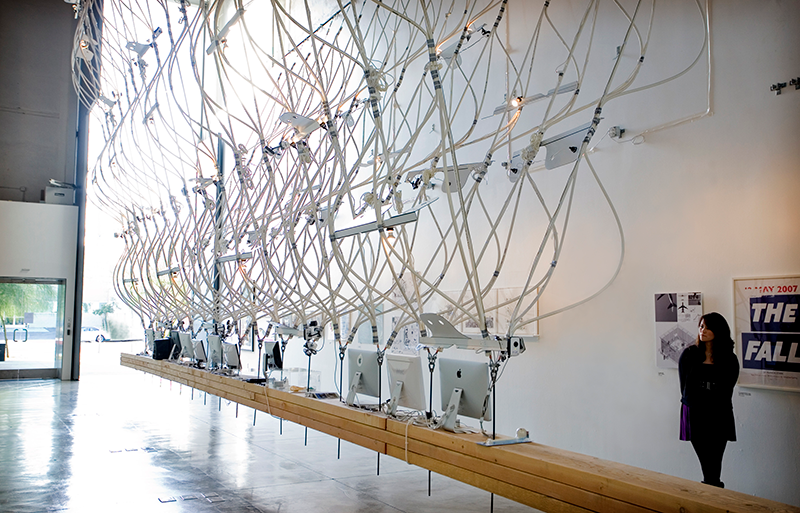